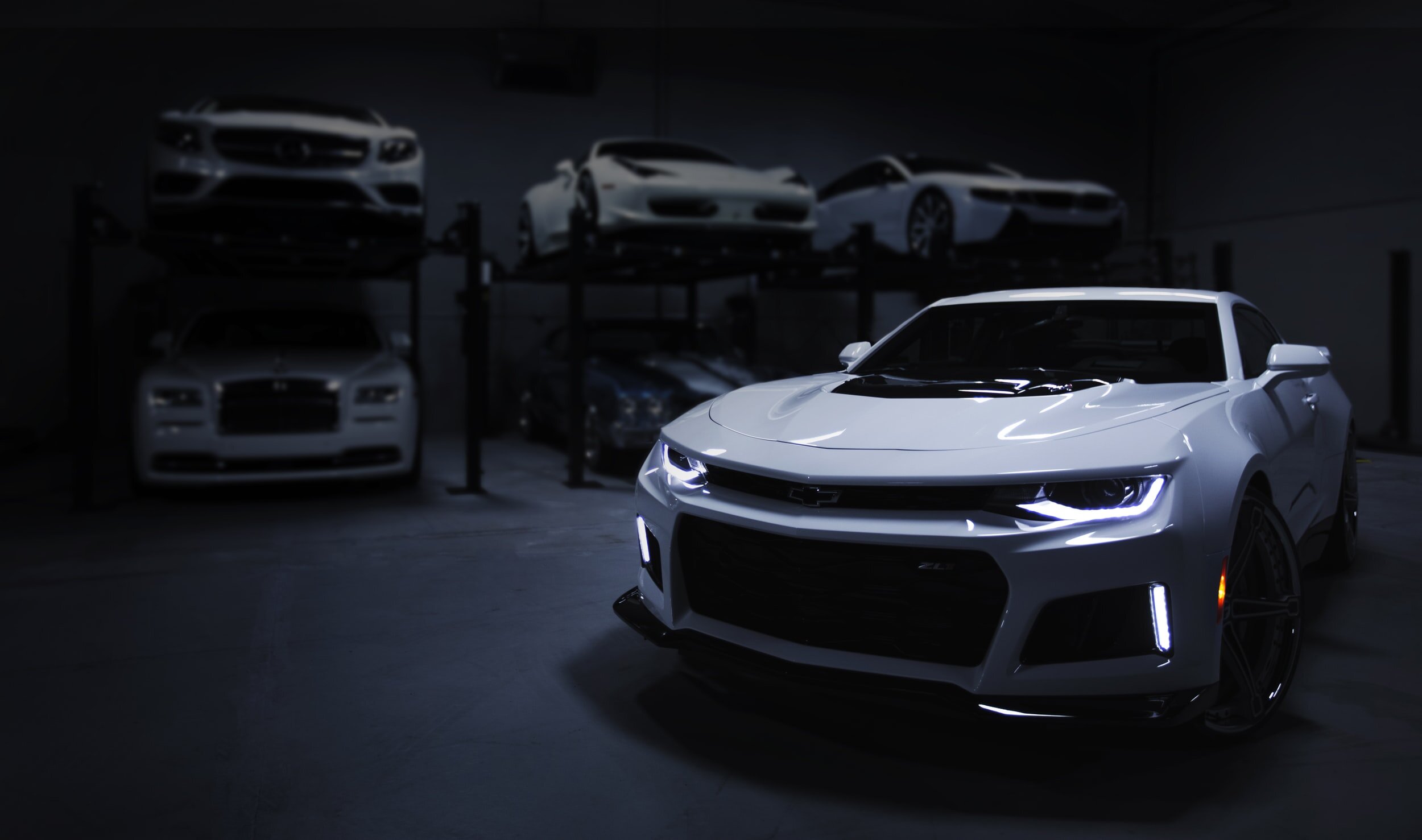
PCS 333: Heat activated alloy wheel stripper.
PCS 333
PCS 333 is a non-methylene chloride hot immersion paint stripper designed to remove wet paint and powder coatings from a variety of substrates. The process minimises the attack on base metals such as aluminium and its alloys and magnesium alloys.
Equipment
All equipment for use with PCS333 should be constructed of 304 or 316 grade stainless steel this will reduce sludge formation on the walls and base of the tank. PCS 333 should have lip or hood extraction. The heating system should be designed to maintain the required temperature and ideally be an oil jacket.
To maintain process efficiency it is essential to ideally clean the tank every 3 months.
All seals and gaskets should be PTFE and Viton must not be used under any circumstances.
Method of operation
PCS 333 is used as received. PCS 333 is operated between 50 and 65 degrees centigrade and the stripping time will depend upon the paint type and film thickness.
If required Performance Chemicals can provide inhibitors for the final rinse to stop corrosion of ferrous substrates.
Tank management
In order to maintain effective stripping the tank must be monitored daily to ensure the chemical is at the desired strength and the tank is free from paint residue which can cause a sludge precipitate if left unmanaged causing particular problems for bottom heated tanks. It is therefore recommended that in addition to the daily chemical checks outlined in the control section below that weekly inspections of the tank are made to check the cleanliness of the tank. It may be necessary to periodically drain and de-sludge the tank.
Control & testing
Daily control of the tank is essential to maintain stripping performance, PCS 333 is consumed during the stripping process and it is important to replenish tank. In order to maintain efficiency and optimum stripping performance it is recommended to top up as follows:
PCS 333 top up ( litres ) = Sets of wheels processed x 2.5
Water top up ( litres ) = Volume Lost - PCS 333 top up
All filtration and de-sludging losses should be made up using PCS 333.
Testing is undertaken to monitor and control the accelerator content. Under normal conditions the PCS 333 will maintain the accelerator pointage however under certain circumtances it will be necesary to raise the accelerator pointage with the addition of PCS 333A. Prior to undertaking the accelerator pointage test it is advisable to top up the tank with PCS 333 as required. Leave to mix for 10 minutes. Take a two ml sample of the tank working solution and add 10ml of water. Add five drops of phenolphthalein and titrate with 0.1N hydrochloric acid from a pink colouration to a clear solution. The number of mls of 0.1N hydrochloric acid used is referred to as the accelerator pointage. The pointage should be between 8.5 - 9.5.
Effluent
PCS 333 Solution must not be discharged to main drainage or storm drainage under any account. The rinse waters should be allowed to run to a settling tank, where heavy solvent and paint residues can settle. A registered Waste Disposal Contractor must dispose of heavy residues together with the main solution.
Safety precautions
When handling PCS 333 wear nitrile rubber gloves, pvc apron, rubber boots and full face protection. Smoking must be prohibited in the vicinity of the PCS 333 plant.
Full information on the hazards and safe handling of the material as supplied is given in the Health and Safety Data Sheet. This must be read and understood fully by those handling or using the product.